By Travis Halsted, ARM, COSS
Loss Control Specialist
As the leaves start to change colors, the temperatures dip at night, and the trick or treaters are developing their gameplan to get the most candy possible, we can’t help but notice that one particular item isn’t changing in our workplaces. That particular item is the need for employees. Temp agencies aren’t producing the number of employees that they were before, applications from potential hires have slowed to a trickle, all while production is starting to increase in several industries. Because of this, companies have turned to their office staff to enter the manufacturing floor, and fill some of the vacant positions. This can prove to be an immediate solution, but without addressing proper training this could also prove to create more challenges.
From Expert to Novice
While the members of your office team may be well versed in the responsibilities of their positions, this doesn’t always mean that they have even the slightest idea of the processes that you have within the other parts of your facility. Nor does it mean that they always have the mechanical abilities to complete some of those processes. Just as you would evaluate the abilities of a new hire, the office employee should also be assessed for their abilities and how/where those abilities fit best. We wouldn’t take an employee from the manufacturing floor and ask them to fill the spot of the CFO, and, while that may be an exaggerated example, it stresses how we shouldn’t naturally assume that the CFO can run equipment, cut material, buff/grind/debur, or even just generally clean the work area. When I entered my first job at a manufacturing facility, I didn’t realize that there is a very noticeable difference in how you mop the floor at home versus how you mop the floor in an oily production environment. I had to be trained on the proper way to mop a floor in that environment. At the same facility I trained an employee that had worked with wood products his entire life and never cut metal on a vertical bandsaw before. He quickly learned that there is a difference between wood and metal. Those were just a couple examples of how what a person may be an expert in, doesn’t always mean it will transition to the manufacturing environment.
Invest in Training
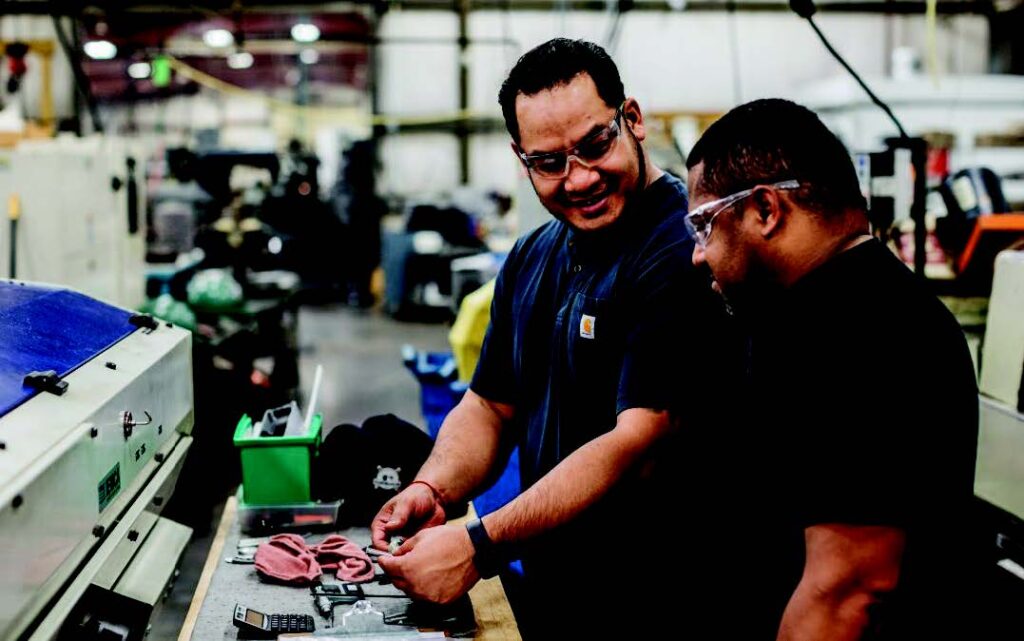
During a recent visit, I had the pleasure of visiting with a young lady that was running a press brake. She had a look of concern on her face and was actually wincing with each press of the foot pedal. She was running a small part that was probably no larger than 5” x 5”. I asked her if everything was alright and she simply replied, “my hands are so close”. I pointed to the tongs that were sitting on the bench by her and recommended using those to hold those parts. I also asked her if she was trained to use those, and the response was a simple no. This was a severe injury waiting to happen. This was a severe claim that was preventable. It turns out that this employee was from purchasing. She buys the material that they bend in that equipment, but it doesn’t mean that she is skilled in operating the equipment. While the employee transitioning from the office to the production floor may have had the trainings on Hazard Communication, Lockout/Tagout, Personal Protective Equipment, etc., they should receive thorough training on the equipment that they will be working with, the hazards of the equipment and materials/chemicals that they will be working with, and the sounds that they may be hearing on the floor (forklift horns, backup beepers, etc.). Furthermore, we should ensure that the office, now production, employee receives appropriate time with the trainer. They should only be left to work alone when they are comfortable with the process and all training is documented. Finally, the employee should be checked on intermittently to ensure that they are still comfortable with the task. We need to remember that these employees do not normally have running equipment in their wheelhouse, and past employment experiences. Lets do our best to add them as a long term asset to your company and not an addition to your loss run.
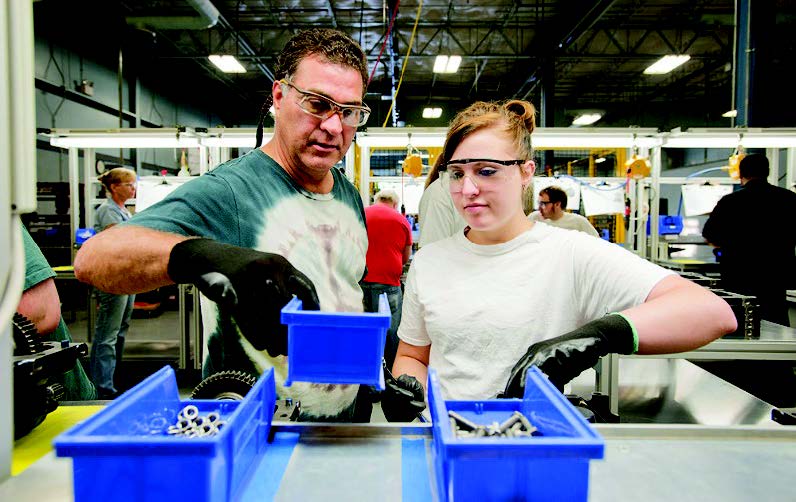
I do have one final note that I wanted to touch on. 2023 has provided me with the unfortunate task of completing several accident investigations. During these investigations I am hearing/reading the root cause as the employee “just wasn’t paying attention”. This may be the event in some situations, but the lack of paying attention is also something that we should delve into. I choose to identify this issue as situational awareness. During one of my investigations, the injury was a finger laceration claim where machine guarding was removed and the employee placed their hand into the point of operation. The employee was injured by the moving parts in said point of operation, and even the employee said that they just weren’t paying attention. When we identify hazards in the workplace, we need to be aware of how an employee may be lacking situational awareness. This employee would not have been able to be injured, paying attention or not, if the guarding was in place. How many near misses have happened in your workplace with forklifts because an employee is not being aware of their environment and walks right out in front of an oncoming forklift? The employee was lacking situational awareness. How can we reduce the likelihood of that lack of situational awareness from becoming a severe event? By installing the blue lights on the front and rear of the forklift to signify its presence it could serve as a trigger to the employee who may be in their own thoughts. Can the accident still occur? Absolutely, but with the light installation, and proper training on the lights, you can provide an additional aspect to combating the situational awareness battle.
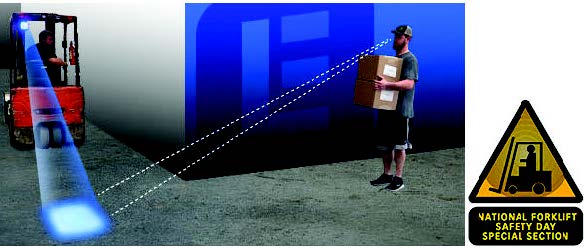
If you have any questions on what employees should be trained on before entering the work environment, or how to identify other ways to reduce to combat poor situational awareness, please do not hesitate to contact your Loss Control Consultant. I hope you all have a safe and happy holiday season!