By Ruth Kiefer, Vice President of Loss Control
With manufacturing in full swing, and limited employee resources, I am sad to say that in recent months, we have had a few severe amputation injuries resulting from employees not using safety die blocks when any body part (fingers, hand, arms, torso, etc.) reaches into a mechanical or hydraulic press. These safety die blocks are required when any body parts are in between the die set, punches, and bolster plates. During these injury events, employees were either making adjustments, troubleshooting, removing parts, or doing die repair and were not using die blocks.
Function of the Safety Blocks:
These safety blocks should be able to support the total static weight of the upper die set, which includes the plate, punches, slides, and all the slide components. You should also have a safety factor of at lest two (2). This means the die block should support the static load 2 times that of what your die set weighs. You may also need more than one die block to hold the weight of your die set. Remember, these blocks are designed to support the static load, NOT the energy and tonnage when a press is under power and cycles. You should be following the lockout tag out instructions for trouble shooting your press if there is a malfunction.
Construction of a Safety Block:
Safety blocks should be made from a strong alloy that will not shatter under the load. Aluminum and magnesium are common materials used for die blocks, of these two common materials used, magnesium is the strongest and is most suitable for heavy loads. Magnesium is also lighter than Aluminum, so when designing or ordering large die blocks, you should consider the weight of the block since employees will need to lift and place these into the press bed. In addition to the construction of the die block, you should also be purchasing die blocks that can be interlocked with the press controls. These interlocks prevent your press from cycling because when your die block is unplugged, the flywheel must come to a rest before placing the block into the press bed.
Lockout, Tag Out
Safety block use should also be part of your lockout/ tagout program. When the ram is raised and there is the potential for the ram to drift or die set components to come down, these safety blocks MUST be in place. I have also seen amputations occur when during a clutch/ break failure, brings the ram down, so the best method to control this potential energy is to use the safety die blocks.
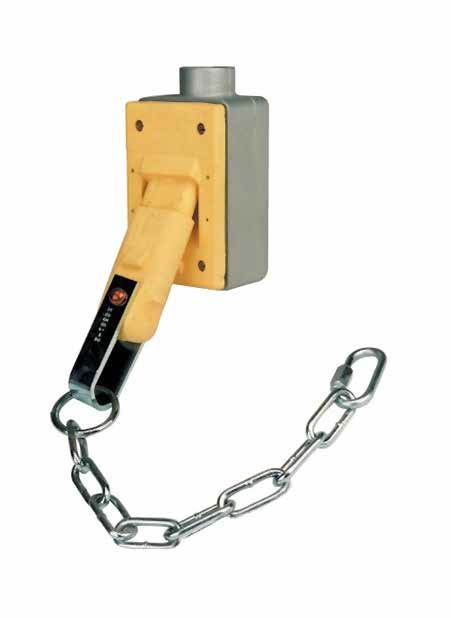
When are Safety Die Blocks Required?
These safety blocks are required anytime a body part enters the die set. I repeat, because, this is how my amputations occur – when die blocks are NOT used. So please, educate, reprimand, encourage the use of die blocks when a body part enters the press. Hand tools should be used for those frequent, but brief times when an employee has to reach into the press for a part or to make a quick adjustment. Your tools can be designed, modified, or fabricated so that they can perform this task. If you cannot fabricate a tool, then guess what? Your employee must use the safety die blocks instead. Why? Because anytime an employees body part enters the die set, safety blocks must be used as a tool cannot reach into this space.
I know you are running full speed, but you also cannot afford to tie up valuable resources, such as your employee or shutting down production because of this type of injury, so please remind your employees the importance of the safety die blocks. If you need further information, we have training materials on our portal in the safety resource section. Or if you have a question, you can always reach out to your loss control consultant, they also know the importance of the safety die blocks and can easily assist you.