By Chris Demeter, Senior Loss Control Consultant
Over the years, I have been in more fab shops than I can remember. The equipment in these shops may vary, but most are equipped with different types of saws, welders, and various pieces of metalworking equipment. One of the most common pieces of metalworking equipment is the power press brake. These metalworking machines bend and form parts through the use of tooling (dies) attached to a ram or slide and a bed. Metal working occurs by placing stock, primarily sheet metal, on a bottom die and pressing it with a top die attached to the movable ram. Press brakes are mechanically or hydraulically powered, or both (hydra-mechanical brakes combine both). Mechanical (flywheel) press brakes use either mechanical friction or air friction clutches that can be disengaged at any point before the crankshaft has completed a full revolution and the press slide has completed a full stroke. By inching and slipping the clutch, these presses allow the operator to drop the slide to the work piece and stop, adjust, or align the work piece, and then complete the stroke. Hydraulic press brakes can normally be stopped at any point in their cycle and the force exerted by the dies can be varied. Operating speeds are normally slower than mechanical presses; however, because of their slower operating speeds they are normally not fully automated. Hydra-mechanical press brakes combine hydraulic and mechanical operations into one system.
Regardless of how the press is powered, the basic operation involves the operator feeding or placing the stock on the bottom die, positioning the stock properly, and activating the press cycle with hand or foot controls. However, one important difference between mechanical and hydraulic brakes is there is no way to reverse the stroke on mechanical brakes. Although it can be stopped or inched, the stroke must be completed. NOTE: When operating a mechanical press brake, if the ram is not brought back up to or past top dead center (crankshaft rotation), the ram may drift back down the wrong way before the clutch re-engages. Not knowing where the ram is in relationship to the stroke is a reason for lost fingers among some press brake operators.
Operating the press brake is only half of the overall operation — the other half involves installing, removing, and transferring the dies.
Hazard
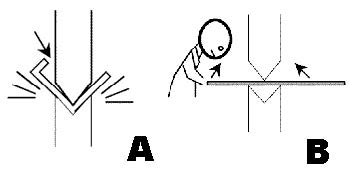
If the press brake can bend metal with ease, it’s obvious that this same capacity can cause serious injuries to operators, including severed or broken arms, hands, fingers, or any other part of the body. Although the actual operation of the press brake does not require the operator to place his or her hands or any part of his or her body into the point of operation, the close exposure to the closing dies still creates a significant risk. In addition, the stock can sometimes “whip” or bend up, creating a pinch-point hazard between it and the front face of the slide (A) or possibly “slapping” the operator if he/she is in the path of the rising material (B).
Installing and removing tooling provides the most direct exposure in the point of operation as the operator must place his or her hands between the two dies. The operator’s hands or arms can be severely crushed if the ram were to fall during setup. Unprotected operating controls, especially foot pedals, can also introduce the possibility of accidental cycling.
Solution
Due to the flexibility needed to fabricate metal on press brakes, it comes as little surprise that these machines are difficult to guard. Fixed or adjustable barrier-type guarding at the point of operation is usually not practical because of the fabrication process (barrier-type guarding can be used to prevent exposure to the unused portions and ends of the tooling). However, feasible safeguarding methods, including presence-sensing devices, two-hand controls, pullbacks, or restraints, can often be used to safeguard the point of operation without reducing productivity.
Presence-sensing devices (light curtains) and two-hand controls are the most common types of press brake safeguarding. A presence-sensing device prevents the machine from cycling when the sensing field is obstructed prior to cycle initiation and stops the down stroke when the sensing field is obstructed after cycle initiation. Twohand controls (palm buttons) are designed to keep the operator’s hands from the die area by requiring concurrent and constant pressure to cycle the machine. Both presencesensing devices and two-hand controls must be located at a proper “safety distance” — the distance from the pinch point hazard so that hazardous motion is stopped or prevented before the operator can enter the point of operation.
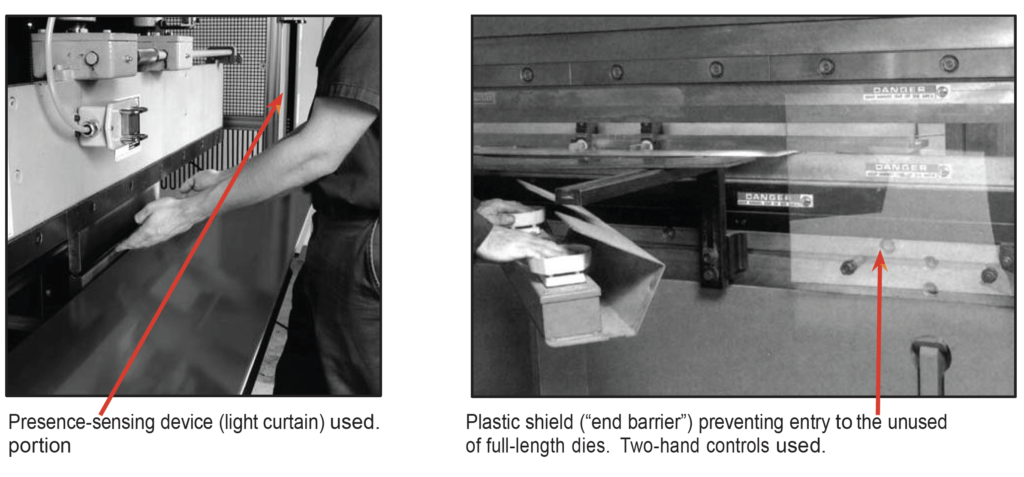
NOTE: When using presence-sensing devices, make sure there is no space between the device and the point of operation where an operator can stand undetected. If this is possible while maintaining an adequate safety distance, additional protection is required such as a second light curtain installed horizontally, a pressure-sensitive mat, or a physical barrier preventing access.
Pullbacks and restraints offer another safeguarding option; these use cables/straps and wristlets to keep the operator’s hands out of the die area by either “pulling back” the arms and hands during the down stroke or simply “restraining” or keeping the operator’s arms and hands from entering the die area. Hand-feeding tools are often necessary when using restraints due to the limited range of movement.
If the use of physical barriers or devices is infeasible, safeguarding by “safe distance” is permitted if the employer meets the conditions described in Oregon OSHA Program Directive #A-217 “Guide-lines for Point of Operation Guarding of Power Press Brakes.” This “Safe Distance Safeguarding” program is limited to one-time-only fabrication of made-to-order or custom-made piece parts, such as small-quantity runs typically performed in “job shop” establishments. A “small-quantity run” means fabrication of more than one of the same piece part over a continuous timeframe of no more than four hours per month.
Under this instruction, the operator and helpers must not approach closer than necessary and in no case, closer than four inches to the brake’s point of operation. The minimum safe distance of four inches must be measured from the exterior point of contact of the brake’s die closest to the worker’s fingers holding and supporting a piece part. Finally, this “Safe Distance Safeguarding” program must contain written expo- sure prevention procedures, training, and enforcement criteria.
If more than one person is needed to operate, only one should be designated as the operator and controls should be furnished for each person. The operator should always make certain that any helpers are clear of the press before beginning the operation. To avoid being pinched or struck by the work piece “whipping” up, never hold the material over the top of a previous bend, keep your hands underneath the work piece, and always keep your face and upper body out of the material’s path.
Before any tooling can be installed, the ram should be locked in the shut height position, with the ram in its most extended position (on the up- stroke). Once the press is locked into that position, the tooling can slide safely into the press. The gap between the ram and the bed should be just big enough to allow easy installation without the tooling falling out. Use safety blocks where tooling permits. Make sure the back gauge is high enough to prevent the piece part from slipping over the top of it, which can bring the operator’s hands and arms into the die. To prevent accidental cycling, effectively cover all hand and foot controls.
As with any power press, a “no hands in die” policy should always be encouraged. Of course, there are times during setup where this exposure will occur and effective die setting procedures or energy-control procedures will address this. Furthermore, the safeguarding devices and strategies mentioned here should keep the operator hands and other body parts out of the die area during operation. Never reach between the tooling for any reason — reach around or walk behind the press brake when necessary. Barricade the back of the press to restrict access.
Safeguarding on these machines has come a long way, but I have also done several accident investigations involving press brakes. Feel free to reach out to your Loss Control Consultant with any questions you have on your press brake or with any other safety questions. With the information presented in this article, consider making it part of your safety manual and training material for your safety committee.
References: General Industry — OSHA Division 2/Subdivision O 29 CFR 1910.212 — General Requirements for All Machines – OSHA Division 2/Subdivision J 29 CFR 1910.147 — The Control of Hazardous Energy(Lockout/Tagout) – OSHA Program Directive A-217 “Guidelines for Point of Operation Guarding of Power Press Brakes” (November 17, 2006) – OSHA Instruction CPL 02-01-025 “Guidelines for Point of Operation Guarding of Power Press Brakes” (February, 14 1997) – ANSI B11.3 Power Press Brakes — Safety Requirements for Construction, Care, and Use – ANSI B11.19 Safeguarding When Referenced by the Other B11 Machine Tool Safety Standards — Performance Criteria for the Design, Construction, Care, and Operation