By Chris Demeter, Senior Loss Control Consultant
Every once in a while my brother will send me a link to a YouTube video of a workplace mishap caught on film. Most of the videos he sends are involving forklifts. They range from a forklift overturning, an unstable load resulting in losing its load, using a forklift improperly to elevate personnel, and forklifes driving into a racking system causing them to fall like a stack of dominoes. This may be riveting to watch, but there is a good chance someone was seriously injured not to mention the thousands of dollars in damage. To put it in perspective, the average automobile weighs approximately 3,000 lbs. and the average forklift not including the load weighs close to 9,000 lbs. To prevent the forklift from tipping forward while lifting a load, forklifts are equipped with a counterweight in the rear of the vehicle. To accommodate narrow aisle and restricted area operations, forklifts are designed with a tight turning radius. With the tight turning radius, it’s common for the rear of the forklift to strike an object such as a storage rack causing damage. It’s common for the damage to go unreported for fear of an employee write-up.
Pallet rack systems are designed for high performance and to support product loads many times their weight. The systems are built to standards that ensure they perform within designed load applications corresponding to the configuration for many years. However, the design specifications and safety factors issued by the pallet racking manufacturer typically do not take into account the loss of capacity and integrity once the pallet racking system has been damaged. Nothing affects the integrity of a pallet rack system like a forklift impact. Operators are not likely to report a collision involving pallet racking structures, so the damage can go undetected. This emphasizes the importance that pallet rack systems be routinely inspected and maintained to the manufacturer and standard specifications to maintain original designed capacity.
Industry Standards
American National Standards Institute (ANSI)
ANSI MH16.1: 2012-Specification for the Design, Testing, and Utilization of Industrial Steel Storage Racks is the industry voluntary consensus standard for industrial pallet rack systems. This standard applies to all industrial pallet rack systems, movable shelf racks, and stacker racks made of cold-formed or hot-rolled steel structural members. It does not apply to other types of racks, such as drive-in or drive-through racks, cantilever racks, portable racks or racks made of a material other than steel. The ANSIMH16.1 has recently been incorporated into the more general International Building Code (IBC). The IBC includes the requirements and governs the construction of all warehouses in the United States. IBC standards must be met to obtain local municipal building permit approval during construction and upon completion. As it relates to inspection and maintenance ANSI MH16.1 states:
- 1.4.1 Owner Maintenance: The racking system operator is responsible for the maintenance and repair of the storage systems
- 1.4.9 Rack Damage: Upon visible damage, the pertinent portions of the rack shall be unloaded immediately and removed from service by the user until the damaged portion is repaired or replaced
Occupational Safety and Health Administration (OSHA)
OSHA Construction standard 1926.250(a)(1): All materials in tiers shall be stacked, racked, blocked or otherwise secured to prevent sliding, falling or collapse. OSHA General Industry standard 1910.176(b): Materials shall not create a hazard.
There is no specific OSHA standard that requires pallet racking to be anchored to the floor, however, they have referenced the General Duty Clause 5(a) (1) to cite employers for pallet racks and other types of industrial steel shelving that is not adequately secured from falling over.
Pallet Rack Inspections
The employer should establish and implement a program of regularly scheduled storage rack system inspections. The inspections should be performed by a qualified person familiar with the storage rack design and installation requirements retained or employed by the storage rack system owner. OSHA defines a qualified person in 29 CFR 1910.21(b): a person who, by possession of a recognized degree, certificate, or professional standing, or who by extensive knowledge, training, and experience has successfully demonstrated the ability to solve or resolve problems relating to the subject matter, the work, or the project. Storage racks should be inspected periodically to check for any damage or abuse and immediately after any event that occurs that may result in damage to the rack. The frequency of inspections is up to the discretion of the owner and dependent on the conditions of use. At a minimum, inspections should be performed annually. The inspection schedule and results of the inspection should be documented and retained. Even if you hire a professional inspector, it is suggested to designate and train someone within the company who will make periodic self-checks of the pallet racking systems. The Rack Manufacturers Institute (RMI) has many resources for inspectors and training curriculum.
What to Inspect
Generally, there are four conditions to inspect pallet racking systems for:
- Plumb and straight
- Load capacity
- Visible rust or corrosion
- Damage
Plumb and straight
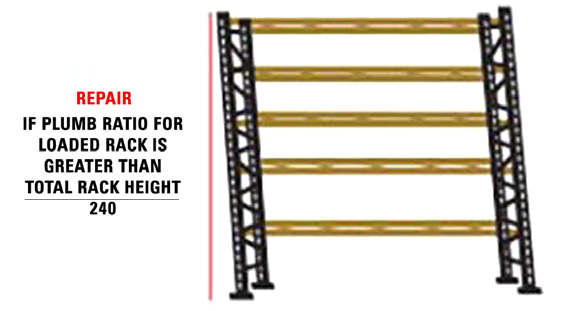
According to ANSI MH16.1-2012, the maximum top to bottom out of the plumb ratio for a loaded rack is Total Rack Height/240 inches (see image 1). For example, a 15 foot (180 inches) column upright height maximum plumb ratio would be 180/240 or ¾ of afoot. This is measured from the centerline of the column upright at the floor to the centerline of the column at the top of the shelf elevation.
Visible rust or corrosion
Any rust or corrosion can indicate weakening metal. If the paint is scraped, a rack may have suffered a collision and should be checked for plumbness and straightness of the upright columns.
Load capacity
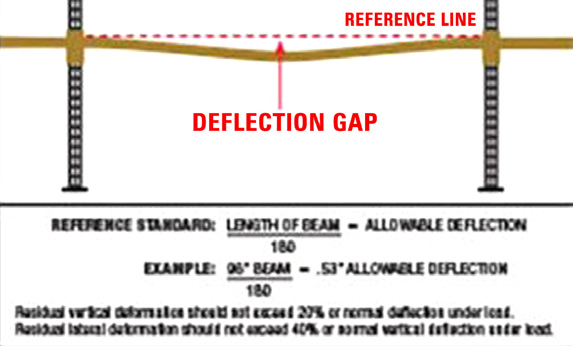
Each manufacturer publishes frame capacity charts. Applicable information should be prominently displayed on a placard at the end of each aisle. Never change the original configuration or weight load without engineering approval. If an approved modification is made, remember to change the placards to reflect the new pallet racking specifications. Overloading can lead to beam deflection. The maximum allowable deflection is the Length of the Beam/180 inches (ANSI MH16.1-2012). Beams should be inspected for deflection gap (see image 2):
Damage
Damage to specific components of a pallet racking system is the most common and serious problem that can affect the integrity of the racking system. The most common components involved in damage are beams, upright columns, and footplate/anchors.
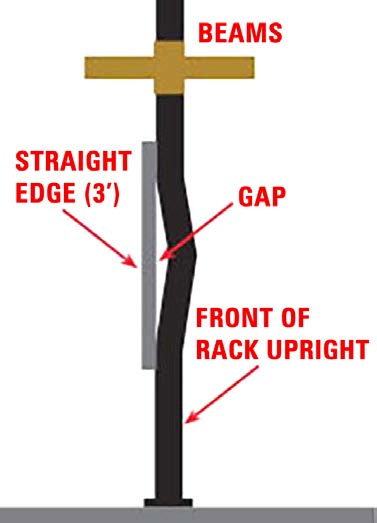
- Beams: Any beam with visible deformation or cracking of the beam end connectors should be unloaded and replaced. Be sure beams are fully engaged and installed with proper safety locks.
- Upright columns: Any rips, tears beyond the manufacturer limits need to be repaired or replaced. Any deflection gap greater than ½ inch (ANSI MH16.1-2012) in either the down aisle or front to back direction must be repaired or replaced. This also includes horizontal and diagonal struts. See image 3.
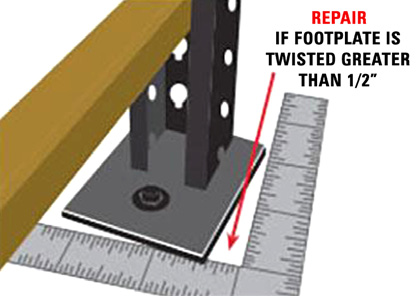
- Footplate/anchors: Any front and back footplates that are torn, ripped, or twisted past ½ inch square. See image 4 below. Each footplate of the upright (front and back) must be anchored to the floor. Check for missing, lose, or sheered anchors.
Note: A trick to measure for damage to upright columns is to place a steel straight edge (ruler or level) on the surface of the concave side of a damaged upright column segment. The straight edge should be centered on the damaged section’s length as accurately as possible. This will allow for a more accurate measure of the gap distance.
Just doing the inspections isn’t enough – you must document and take action when needed. Documentation helps you track the regularity and thoroughness of the inspection process in the event of any future issue. If you hire an inspector, be sure they adhere to the industry or local code standards and they also document and retains the records of their inspections. Please note that these tips are just for informational purposes; see a rack inspection professional to ensure that your facility is safe and that your rack is in no danger of failure. If you chose to perform your inspections in-house, a racking inspection template checklist can be found on the MTMIC online client portal under documents.
Over the years, I have performed thousands of safety walkthroughs. During loss control visits with accounts with pallet racking systems, it’s common to find damage at the base of a storage rack leg. This is usually from the load bumping the base leg because it’s not being squarely placed on the rack. I will recommend to prevent future damage to your storage rack legs, storage rack leg protectors can be purchased at a number of companies online. The storage rack leg protectors are made of heavy gauge metal and anchored to the floor; they will help prevent damage to the leg if bump into. Should any damage or other unsafe condition be discovered, the racking should be immediately unloaded and repaired under the guidance of a qualified professional rack engineer to assess the rack’s condition and oversee the ultimate repair or replacement. I strongly encourage you to contact your Loss Control Consultant to discuss any pallet racking questions and/or concerns. A good part of my job is driving from one account to another. I must say this winter has not been that bad with temperatures and bad roads, except for the potholes. By the time you read this newsletter, we should be getting into some milder temperatures and more potholes. Think Spring!